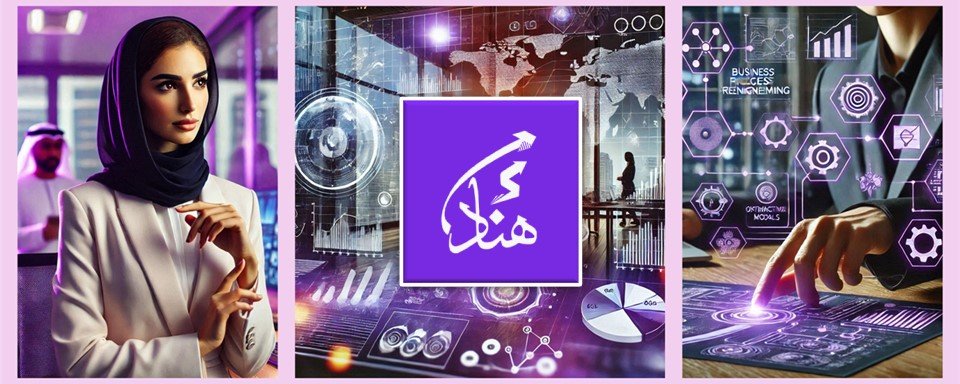
Kanban System Design and Implementation
By the end of this course, participants will have the skills to design, implement, and manage a Kanban system tailored to their organization’s needs. With a focus on optimizing workflow, controlling work-in-progress, and fostering a culture of continuous improvement, Kanban empowers teams to improve efficiency, deliver better results, and achieve higher customer satisfaction. This course equips participants with practical knowledge and tools to apply Kanban to a wide variety of industries, from software development to manufacturing, services, and beyond.
Introduction:
Kanban is a visual workflow management method that helps teams improve efficiency, reduce waste, and increase productivity. It originated in the manufacturing sector but has since been adapted across various industries to manage projects, tasks, and services. This course covers the design and implementation of Kanban systems for workflow optimization, helping organizations manage work in progress (WIP) and drive continuous improvement. Participants will learn how to create a Kanban system, visualize work, and use it to manage and improve processes in their organizations.
Targeted Groups:
- Project Managers
- Team Leaders and Supervisors
- Process Improvement Specialists
- Operations Managers
- Agile Coaches and Scrum Masters
- Business Analysts
- Workflow and Operations Teams
- Individuals involved in service delivery and production systems
Course Objectives:
By the end of this course, participants will be able to:
- Understand the core principles and practices of the Kanban methodology.
- Design and implement Kanban systems to optimize workflow and increase team productivity.
- Visualize processes, track work, and manage work-in-progress (WIP).
- Apply the Kanban system to various environments, including software development, manufacturing, and services.
- Implement WIP limits to control capacity and enhance process flow.
- Use metrics and data to improve the system continuously.
- Align team efforts to reduce bottlenecks and improve throughput.
Targeted Competencies:
- Workflow Management
- Process Optimization
- Continuous Improvement (Kaizen)
- Visual Management
- Work-in-Progress (WIP) Control
- Team Collaboration and Communication
- Agile and Lean Practices
- Problem-Solving and Bottleneck Identification
- Performance Metrics and Analytics
- Kanban System Metrics and Reporting
Course Content:
Unit 1: Introduction to Kanban
- Understanding the origins and evolution of Kanban.
- The core principles of Kanban: Visualizing work, limiting WIP, managing flow, making process policies explicit, and improving collaboratively.
- Benefits of Kanban: Efficiency, flexibility, and continuous delivery.
- Comparing Kanban to other workflow management methodologies (e.g., Scrum, Lean).
- Key terms and concepts in Kanban: Workflow, WIP limits, lead time, cycle time, throughput, bottlenecks, and flow efficiency.
- Real-world examples of Kanban applications in various industries.
Unit 2: Designing a Kanban System
- Mapping your workflow: Understanding current processes and identifying opportunities for improvement.
- Designing the Kanban board: Components of a Kanban board (columns, cards, WIP limits).
- Types of Kanban boards: Physical boards vs. digital tools (e.g., Trello, Jira, Kanbanize).
- Creating a flow diagram to map tasks, milestones, and decision points.
- Defining process policies and rules to ensure smooth flow of work.
- Choosing appropriate WIP limits for different workflow stages.
- Aligning the Kanban system with team and organizational goals.
Unit 3: Implementing Kanban Systems
- Initial setup: Steps for implementing a Kanban system within an existing process.
- Setting up a Kanban board: Design considerations, placement, and visibility.
- Identifying and organizing work items: Types of work items and classification (e.g., user stories, tasks, bugs).
- Establishing WIP limits: Balancing capacity with demand to avoid bottlenecks.
- Conducting daily stand-ups and visual management practices.
- Creating pull systems: How work items are “pulled” through the system rather than pushed.
- Assigning roles and responsibilities in Kanban: Team members’ roles in managing and using the system.
Unit 4: Managing Flow and Improving Performance
- Understanding the flow of work and cycle time.
- Identifying bottlenecks: Recognizing and addressing flow disruptions.
- Monitoring flow efficiency: Key performance indicators (KPIs) like lead time, cycle time, and throughput.
- Analyzing and reducing delays in the workflow.
- Continuous improvement using Kaizen: How to apply iterative improvements to the system.
- Collecting data to inform decisions and improve flow.
- Strategies for balancing workload across teams.
- How to use metrics to improve work distribution and throughput.
Unit 5: Advanced Kanban Techniques
- Scaling Kanban: Implementing Kanban in large teams or multi-team environments.
- Kanban for services vs. production: Adapting Kanban systems for different types of work.
- Managing multiple Kanban boards: Synchronizing boards for cross-team collaboration.
- Feedback loops and continuous feedback mechanisms.
- Advanced metrics for Kanban: Cumulative flow diagrams (CFDs), cycle time distribution, and flow efficiency.
- Using Kanban to manage dependencies and cross-functional collaboration.
- Integrating Kanban with other Agile practices (e.g., Scrum, Lean).
- Applying Kanban to non-software environments (e.g., marketing, HR, manufacturing).
Unit 6: Kanban System Evaluation and Continuous Improvement
- Reviewing and evaluating Kanban system performance: Using data and metrics to assess system effectiveness.
- Identifying opportunities for system optimization and process redesign.
- Improving the Kanban board based on team feedback and metrics.
- Implementing regular retrospectives for Kanban systems.
- How to use root cause analysis for persistent problems in the workflow.
- Handling resistance to Kanban implementation within teams or organizations.
- Adjusting WIP limits and board configurations as teams grow or needs change.
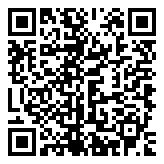