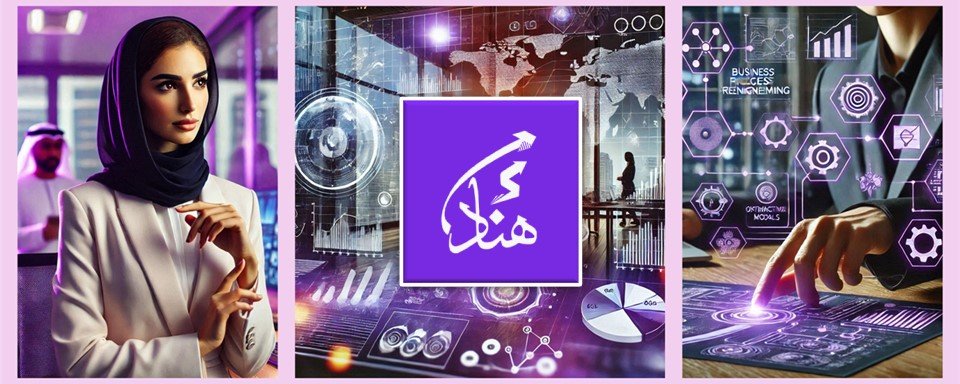
تقنيات مراقبة الجودة للمديرين
ال تقنيات مراقبة الجودة للمديرين course equips participants with the practical knowledge and tools to drive quality improvement within their organizations. By mastering quality control techniques like SPC, Six Sigma, and Lean, managers can ensure that their products and services consistently meet customer expectations, reduce waste, and foster continuous improvement. Upon completion, participants will be empowered to lead quality initiatives, monitor performance, and create a culture of excellence within their teams.
مقدمة:
Effective quality control is a cornerstone of business success, ensuring that products and services meet the required standards and satisfy customer expectations. The تقنيات مراقبة الجودة للمديرين course is designed to provide managers with the tools and knowledge to implement and maintain high-quality standards across their organizations. Participants will explore the principles and methodologies behind quality control, as well as techniques to monitor, measure, and improve product and service quality. By mastering quality control, managers can reduce defects, enhance customer satisfaction, and improve operational efficiency.
This course focuses on the practical application of quality control methods, ensuring that managers are equipped to implement improvements and measure outcomes effectively. Participants will gain a deeper understanding of how quality control fits into the broader context of quality management systems and continuous improvement.
الفئات المستهدفة:
- مديري العمليات
- Quality Managers and Engineers
- Production Supervisors
- مديري المشاريع
- Process Improvement Teams
- مديري سلسلة التوريد والخدمات اللوجستية
- Product Development Managers
- Customer Service Managers
- Compliance and Regulatory Managers
- محللون ومستشارون للأعمال
أهداف الدورة:
في نهاية هذه الدورة، سيكون المشاركون قادرين على:
- Understand the importance of quality control in business and its impact on customer satisfaction and profitability.
- Apply key quality control techniques, such as statistical process control (SPC), Six Sigma, and lean management.
- Use various tools like control charts, Pareto analysis, and root cause analysis to monitor and improve processes.
- Develop strategies for improving quality across different business functions (manufacturing, service, etc.).
- Implement corrective and preventive actions to address quality issues and prevent recurrence.
- Understand the role of quality control within a larger quality management system (QMS).
- Communicate quality control findings and recommendations effectively to key stakeholders.
الكفاءات المستهدفة:
- التحكم الإحصائي في العمليات (SPC)
- تحليل السبب الجذري وحل المشكلات
- Process Monitoring and Measurement
- Corrective and Preventive Actions (CAPA)
- Lean Manufacturing and Six Sigma Techniques
- Quality Management System (QMS) Implementation
- Process Optimization and Continuous Improvement
- Supplier Quality Management
- Risk Assessment and Quality Assurance
- Effective Communication of Quality Data
محتوى الدورة:
Unit 1: Introduction to Quality Control
- Defining quality control and its role in business success
- The difference between quality control, quality assurance, and quality management
- The cost of poor quality and the benefits of effective quality control
- Key quality standards: ISO 9001, Six Sigma, and other industry-specific standards
- The relationship between customer expectations and product/service quality
- Case study: How effective quality control improved a product line’s customer satisfaction and reduced returns
Unit 2: Key Quality Control Techniques
- Statistical Process Control (SPC): Using data to monitor and control process variability
- Control charts: Types (X-bar, R, P, NP) and how to use them effectively
- Process Capability Analysis: Measuring the capability of a process to meet specification limits
- Pareto Analysis: Identifying the most significant problems and focusing efforts on the 80/20 rule
- Failure Mode and Effects Analysis (FMEA): Identifying and prioritizing potential risks in the process
- Scatter Diagrams and Correlation Analysis: Visualizing relationships between variables
- Case study: Implementing SPC in a manufacturing plant to reduce defects and improve consistency
Unit 3: Lean and Six Sigma for Quality Control
- Overview of Lean principles: Waste reduction and process efficiency
- Six Sigma methodology: Define, Measure, Analyze, Improve, and Control (DMAIC)
- Key tools for Six Sigma: Fishbone diagrams, process mapping, and 5 Whys
- Integrating Lean and Six Sigma for process improvement and quality control
- Value stream mapping: Identifying and eliminating waste in processes
- Case study: A Six Sigma project that reduced cycle time and improved customer satisfaction
Unit 4: Process Monitoring and Measurement
- Understanding process variability and how it impacts quality
- Setting up key performance indicators (KPIs) for monitoring quality
- Using process maps and flowcharts to identify critical control points
- How to measure quality: Defects per unit (DPU), defects per million opportunities (DPMO), and yield rates
- Benchmarking: Comparing processes to industry standards and best practices
- Case study: Setting up a process monitoring system to track product quality in real time
Unit 5: Root Cause Analysis and Problem-Solving
- The importance of identifying the root cause of quality issues
- Techniques for root cause analysis: 5 Whys, Fishbone diagrams (Ishikawa), and Fault Tree Analysis
- Implementing corrective and preventive actions (CAPA) to address the root cause
- Problem-solving frameworks: A3 Problem Solving and PDCA (Plan-Do-Check-Act)
- Ensuring that solutions are sustainable and aligned with long-term quality goals
- Case study: A root cause analysis of a recurring quality issue and the corrective actions taken
Unit 6: Corrective and Preventive Actions (CAPA)
- Defining CAPA: The role of corrective and preventive actions in quality management
- Corrective actions: Addressing immediate quality problems and preventing recurrence
- Preventive actions: Identifying and mitigating risks before they cause quality issues
- Implementing CAPA within the quality management system (QMS)
- How to track and verify the effectiveness of CAPA initiatives
- Case study: Implementing a CAPA system to address a compliance failure in the pharmaceutical industry
Unit 7: Supplier Quality Management
- The role of suppliers in maintaining product quality
- Establishing supplier quality requirements and monitoring performance
- Auditing suppliers: Conducting regular quality audits and assessments
- Developing strong supplier relationships to ensure consistent quality
- Risk management: Identifying and managing risks related to suppliers and external partners
- Case study: How supplier quality management helped a company ensure consistent product quality
Unit 8: Communicating Quality Control Findings
- The importance of clear communication in quality control processes
- How to create effective quality control reports for management, teams, and clients
- Visualizing quality data: Using graphs, charts, and dashboards to present findings
- Providing actionable recommendations based on quality analysis
- Communicating with cross-functional teams to ensure alignment on quality objectives
- Case study: Effective communication of quality control results leading to process improvements
Unit 9: Continuous Improvement and Sustainability
- The principles of continuous improvement and its connection to quality control
- Developing a culture of quality and continuous improvement in your organization
- How to measure and sustain improvements over time
- Tools for fostering innovation and ongoing quality enhancements: Kaizen, Total Quality Management (TQM)
- Best practices for sustaining quality control improvements across departments
- Case study: A continuous improvement initiative that led to a sustained increase in product quality
Final Project and Quality Control Plan:
- Participants will develop a detailed quality control plan for their organization or a hypothetical scenario.
- The plan will include key quality control techniques, process monitoring systems, root cause analysis, CAPA strategies, and a sustainability plan for ongoing improvement.
- Participants will present their plan for peer feedback and refinement.
التقييم النهائي والشهادة:
- Review of key quality control concepts covered throughout the course
- تمارين عملية واختبارات وعمل جماعي لتعزيز التعلم
- العرض النهائي للمشروع وتقييم الأقران
- يتم منح الشهادة عند إكمال الدورة بنجاح
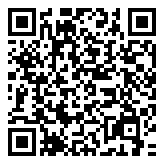