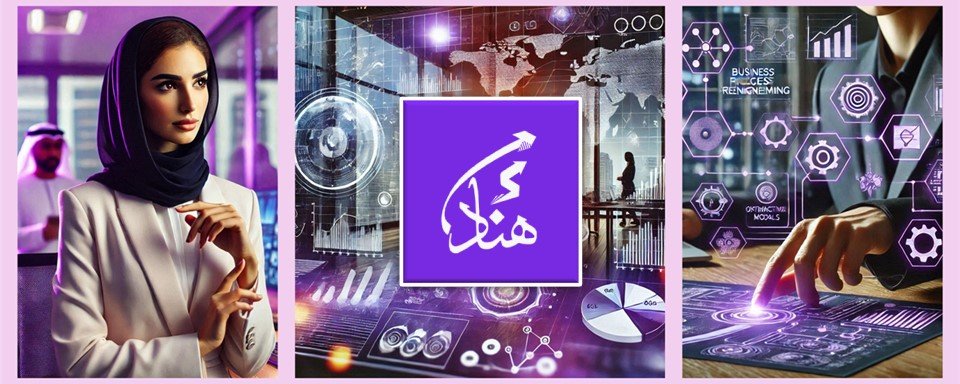
تحليل السبب الجذري وحل المشكلات
ال تحليل السبب الجذري وحل المشكلات course provides professionals with the tools, techniques, and strategies needed to solve problems at their root cause and implement effective, sustainable solutions. By mastering RCA methodologies such as 5 Whys, Fishbone diagrams, and FMEA, participants will be able to improve process efficiency, reduce defects, and contribute to continuous improvement in their organizations. This course equips participants to lead problem-solving efforts, communicate findings effectively, and drive long-term organizational success.
مقدمة:
Effective problem-solving is at the heart of continuous improvement and operational excellence in any organization. The تحليل السبب الجذري وحل المشكلات course is designed to provide professionals with the tools and techniques to identify the underlying causes of issues, resolve problems at their source, and implement sustainable solutions. By mastering the art of root cause analysis (RCA), participants will be able to reduce repeat incidents, optimize processes, and drive long-term improvement across various business functions.
The course covers a wide array of root cause analysis methods and provides participants with practical skills for applying them in real-world scenarios. Attendees will learn to use systematic approaches to investigate complex problems, identify root causes, and implement corrective actions that prevent recurrence.
الفئات المستهدفة:
- Problem Solvers and Process Improvement Teams
- Quality Control and Assurance Managers
- Operations Managers and Supervisors
- ممارسو لين وستة سيجما
- Product Development and Engineering Teams
- Customer Service Managers
- مديري المشاريع
- Maintenance and Production Staff
- Continuous Improvement Leaders
- المستشارون ومحللو الأعمال
أهداف الدورة:
في نهاية هذه الدورة، سيكون المشاركون قادرين على:
- Understand the principles and importance of root cause analysis in problem-solving.
- Apply various RCA methodologies, including the 5 Whys, Fishbone diagram (Ishikawa), and Failure Mode and Effects Analysis (FMEA).
- Investigate problems systematically to identify their root causes rather than treating symptoms.
- Use data and evidence to support the analysis and ensure accurate problem identification.
- Develop effective corrective actions and solutions that address the root cause and prevent recurrence.
- Implement a structured problem-solving approach that can be applied across different business functions and industries.
- Foster a problem-solving culture within teams and organizations to drive continuous improvement.
الكفاءات المستهدفة:
- Root Cause Analysis Techniques
- Problem-Solving Methodologies
- Process Mapping and Flowcharting
- Data Collection and Analysis for Problem Solving
- Corrective and Preventive Actions (CAPA)
- Failure Mode and Effects Analysis (FMEA)
- Failure Analysis and Fault Tree Analysis
- Lean and Six Sigma Problem-Solving Tools
- Continuous Improvement and Change Management
- Team Collaboration and Communication Skills
محتوى الدورة:
Unit 1: Introduction to Root Cause Analysis and Problem Solving
- The importance of solving problems at their root cause
- The difference between symptoms and root causes
- Overview of problem-solving models and frameworks
- How RCA fits into the broader context of continuous improvement and quality management
- Key principles of problem-solving: Systematic, data-driven, and collaborative
- Case study: How addressing root causes eliminated recurring operational issues in a manufacturing process
Unit 2: Key Root Cause Analysis Methodologies
- 5 Whys Analysis: A simple and effective technique for identifying the root cause by asking “why” repeatedly
- مخطط هيكل السمكة (إيشيكاوا): A visual tool for categorizing and identifying potential causes of a problem
- تحليل وضع الفشل وتأثيراته (FMEA): A proactive approach for identifying potential failures in a process before they occur
- تحليل باريتو: Using the 80/20 rule to identify the most significant causes of problems
- Fault Tree Analysis (FTA): A top-down approach for analyzing failure events and their contributing factors
- Histogram and Scatter Diagram: Visual tools for identifying correlations and patterns in data
- Case study: A company’s use of Fishbone diagrams to uncover causes of customer complaints in a service department
Unit 3: Data Collection and Analysis for Root Cause Identification
- The importance of data in RCA: Gathering relevant, accurate, and sufficient data
- Types of data: Qualitative vs. quantitative data
- Methods for collecting data: Surveys, interviews, observation, and document review
- Analyzing data: Identifying trends, patterns, and anomalies
- Tools for analyzing data: Statistical Process Control (SPC), Pareto charts, and histograms
- Case study: Using data analysis to solve a problem in the supply chain and reduce delivery delays
Unit 4: Investigating the Problem and Identifying Root Causes
- Structuring the problem-solving process: Identifying the problem, collecting evidence, and analyzing data
- Root cause investigation techniques: Brainstorming, brainstorming with team involvement, and expert input
- Understanding the problem within the broader system: Considering all contributing factors, including process, people, policies, and materials
- Identifying direct and indirect causes of the problem
- Recognizing cognitive biases and pitfalls that can influence the investigation process
- Case study: A root cause investigation into a production line failure and the underlying organizational factors that contributed to it
Unit 5: Developing and Implementing Corrective Actions
- Defining corrective actions: Solutions that address the root cause and prevent recurrence
- Corrective vs. preventive actions: Ensuring actions fix the problem and prevent similar problems in the future
- Developing a corrective action plan: Key steps for implementing solutions, including timeline, resources, and responsibilities
- Testing corrective actions: Verifying the effectiveness of the solution before full implementation
- Monitoring and evaluating the outcome: Ensuring the problem does not recur and that the solution is sustainable
- Case study: Implementing corrective actions to reduce defects in a quality control process and ensuring long-term sustainability
Unit 6: Continuous Improvement and Preventive Action
- Moving from corrective to preventive actions: Preventing problems before they occur
- Building a culture of continuous improvement: Encouraging proactive problem solving and RCA throughout the organization
- Integrating RCA into broader quality management systems (QMS)
- Using RCA results for process optimization and improvement
- Learning from failures: How to create a feedback loop to prevent similar issues from arising
- Case study: A lean manufacturing plant’s efforts to continuously improve its processes using RCA and preventive actions
Unit 7: Communication and Collaboration in Problem Solving
- The importance of effective communication during the problem-solving process
- Collaborative problem solving: Involving stakeholders and team members in identifying and solving problems
- Presenting problem-solving results: Communicating root causes, corrective actions, and lessons learned to stakeholders
- Creating a problem-solving culture: Encouraging open communication, transparency, and shared responsibility for solutions
- Techniques for leading problem-solving meetings and workshops
- Case study: How a cross-functional team successfully solved a supply chain issue through effective communication and collaboration
Unit 8: Best Practices in Root Cause Analysis and Problem Solving
- Best practices for ensuring effective root cause analysis and problem-solving across the organization
- Developing problem-solving skills within teams: Training, mentoring, and knowledge sharing
- Ensuring consistency in the RCA process: Standardizing approaches and templates for problem-solving
- Avoiding common pitfalls: Confirmation bias, jumping to conclusions, and focusing on symptoms
- Establishing metrics for evaluating the success of root cause analysis and corrective actions
- Case study: A global company’s approach to embedding RCA as a core competency across all departments
Final Project and RCA Plan:
- Participants will work on a real-world problem or case study and apply the root cause analysis methodologies learned throughout the course.
- They will create an action plan that includes data collection, RCA methodologies, root cause identification, corrective actions, and implementation strategies.
- Participants will present their findings and solutions to the class for feedback.
التقييم النهائي والشهادة:
- Review of the core RCA concepts and tools
- Practical exercises and group discussions to reinforce learning
- العرض النهائي للمشروع والتقييم
- يتم منح الشهادة عند إكمال الدورة بنجاح
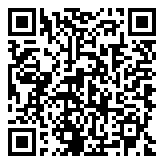