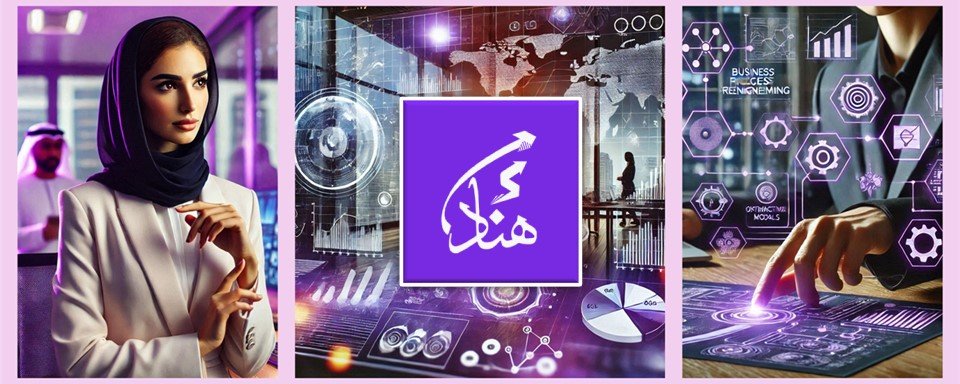
Operational Efficiency Best Practices
Participants in the Operational Efficiency Best Practices course will gain the skills and knowledge to identify inefficiencies, optimize processes, and create a culture of continuous improvement. By implementing best practices and leveraging Lean and Six Sigma methodologies, participants will help their organizations achieve higher productivity, cost savings, and customer satisfaction.
Introduction:
Operational efficiency is key to maintaining a competitive edge, reducing costs, and maximizing value in any organization. By optimizing processes, improving resource management, and eliminating waste, businesses can improve productivity and profitability while delivering superior value to customers.
The Operational Efficiency Best Practices course is designed to equip participants with the strategies and tools to optimize operations across various functions. The course will cover proven methodologies, frameworks, and techniques for improving efficiency, streamlining workflows, and driving operational excellence. Participants will gain the knowledge and skills to implement best practices that enhance performance and contribute to long-term success.
Targeted Groups:
- Operations Managers and Directors
- Process Improvement Specialists
- Supply Chain and Logistics Managers
- Quality Assurance and Control Professionals
- Business Analysts
- Senior Executives and Business Leaders
- Lean and Six Sigma Practitioners
- Consultants and Change Management Specialists
Course Objectives:
By the end of this course, participants will be able to:
- Understand the principles and benefits of operational efficiency.
- Identify key areas of inefficiency within an organization.
- Implement lean methodologies and process improvement techniques.
- Streamline workflows to optimize resource use and reduce waste.
- Utilize technology and automation to enhance operational performance.
- Establish performance metrics and KPIs to track operational efficiency.
- Drive continuous improvement and foster a culture of operational excellence.
Targeted Competencies:
- Process Optimization
- Resource Management
- Lean and Six Sigma Methodologies
- Performance Measurement and KPIs
- Cost Reduction Strategies
- Operational Risk Management
- Continuous Improvement and Innovation
Course Content:
Unit 1: Introduction to Operational Efficiency
- Definition and importance of operational efficiency
- Key drivers of inefficiency in organizations
- How operational efficiency impacts profitability and customer satisfaction
- Case studies of organizations that have achieved operational excellence
Unit 2: Identifying Inefficiencies and Bottlenecks
- Conducting process assessments and mapping workflows
- Techniques for identifying inefficiencies and waste (e.g., Value Stream Mapping, SWOT Analysis)
- Tools for recognizing bottlenecks in operations
- Common sources of inefficiency and how to address them
Unit 3: Lean Methodology and Waste Reduction
- Principles of Lean: eliminating waste, continuous improvement, and respecting people
- The 5S framework for workplace organization
- Value Stream Mapping to identify and eliminate non-value-added activities
- Kaizen and its role in continuous improvement
- Practical applications of Lean in different industries
Unit 4: Six Sigma and Process Improvement
- Introduction to Six Sigma methodology (DMAIC)
- Identifying and eliminating defects in processes
- Data-driven decision making for process improvement
- Using statistical tools for process analysis and control
- Real-world examples of Six Sigma implementation
Unit 5: Automation and Technology for Operational Efficiency
- Role of technology and automation in improving efficiency
- Identifying opportunities for automation in routine processes
- Software tools for workflow automation and process management
- Implementing artificial intelligence and machine learning to optimize operations
- Benefits and challenges of adopting new technologies in operations
Unit 6: Resource Optimization and Cost Control
- Managing human, financial, and physical resources effectively
- Techniques for inventory optimization and just-in-time (JIT) systems
- Lean principles for cost reduction without sacrificing quality
- Energy efficiency and sustainability in operations
- Balancing cost control with service excellence
Unit 7: Performance Metrics and KPIs for Operational Efficiency
- Defining key performance indicators (KPIs) for operations
- Metrics to track productivity, cycle time, and resource utilization
- Setting benchmarks for operational performance
- Data collection and reporting for decision-making
- Using dashboards and scorecards to track operational success
Unit 8: Continuous Improvement and Building a Culture of Efficiency
- Establishing a continuous improvement mindset across all levels of the organization
- Engaging employees in process optimization initiatives
- Tools and techniques for fostering innovation and problem-solving (e.g., PDCA, Root Cause Analysis)
- The role of leadership in driving operational excellence
- Building a culture of collaboration, accountability, and performance excellence
Unit 9: Change Management and Overcoming Resistance
- Managing organizational change to support efficiency initiatives
- Addressing resistance to process changes and new technologies
- Communication strategies for successful change management
- Building stakeholder buy-in for operational efficiency initiatives
Unit 10: Case Studies and Best Practices
- Real-world examples of companies that have achieved operational excellence
- Lessons learned from successful and challenging efficiency initiatives
- Industry-specific best practices and benchmarks for operational improvement
Final Project and Action Plan Development
- Developing a personalized action plan to improve operational efficiency in participants’ organizations
- Identifying key areas for improvement and defining action steps
- Setting timelines, responsibilities, and performance metrics for improvement initiatives
- Peer feedback and collaborative review of action plans
Final Assessment and Certification:
- Review and application of operational efficiency principles
- Practical exercises, case study analysis, and group discussions
- Final project presentation and action plan evaluation
- Certification awarded upon successful completion
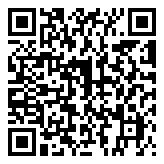