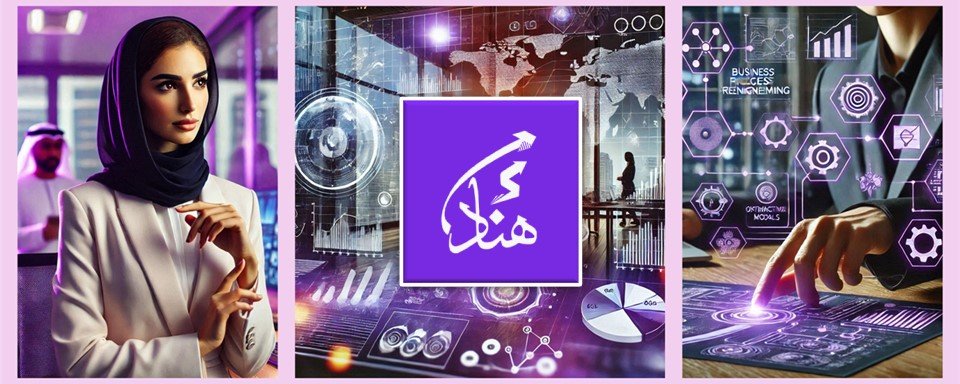
Quality Auditing for Continuous Improvement
The Quality Auditing for Continuous Improvement course equips participants with the necessary tools and techniques to conduct effective quality audits that drive improvement. By understanding how to assess processes, identify non-conformities, and implement corrective actions, participants will be able to play a key role in fostering a culture of continuous improvement. This course prepares professionals to enhance organizational performance, achieve compliance, and contribute to long-term success through effective quality management practices.
Introduction:
Quality auditing plays a vital role in ensuring that organizational processes and operations meet established standards and are continuously improving. This course will explore the principles and practices of quality auditing, focusing on how to assess the effectiveness of quality management systems and identify opportunities for continuous improvement. The goal is to provide participants with the knowledge and skills to conduct audits that drive organizational success, identify weaknesses, and foster a culture of excellence. Quality audits not only help ensure compliance but also enable organizations to refine processes, improve product quality, and increase customer satisfaction.
Targeted Groups:
- Quality Managers and Quality Assurance Professionals
- Internal and External Auditors
- Process Improvement Specialists
- Compliance and Regulatory Officers
- Risk Managers and Analysts
- Operations Managers and Team Leaders
- Lean Six Sigma and Continuous Improvement Teams
- Senior Executives and Decision Makers
- Consultants and Trainers in Quality Management
- Supply Chain Managers
Course Objectives:
By the end of this course, participants will be able to:
- Understand the purpose and scope of quality audits within quality management systems (QMS).
- Learn the key principles of auditing for continuous improvement and process optimization.
- Conduct internal and external audits to assess the effectiveness of processes, products, and systems.
- Identify non-conformities, gaps, and opportunities for improvement through audits.
- Develop audit reports and provide actionable recommendations for improvement.
- Apply risk-based thinking to auditing practices to ensure that critical areas are prioritized.
- Use audit findings to drive corrective and preventive actions (CAPA).
- Implement auditing as a tool for achieving long-term quality improvement and compliance.
Targeted Competencies:
- Quality Management Systems (QMS)
- Audit Planning and Execution
- Root Cause Analysis and Problem-Solving
- Corrective and Preventive Action (CAPA)
- Risk Assessment and Management
- Continuous Improvement Methodologies (e.g., Lean, Six Sigma)
- Process Optimization
- Data Analysis and Reporting
- Compliance and Regulatory Standards (ISO, IATF, etc.)
- Stakeholder Communication and Engagement
Course Content:
Unit 1: Introduction to Quality Auditing
- Overview of quality auditing and its role in continuous improvement
- The relationship between quality audits and quality management systems (QMS)
- Types of audits: Internal, external, compliance, process, and product audits
- Key auditing principles: Objectivity, independence, and evidence-based assessment
- Benefits of quality auditing: Identifying inefficiencies, improving processes, and ensuring compliance
- Case Study: A review of a real-world quality audit and its impact on process improvement
Unit 2: Auditing Standards and Methodologies
- Common auditing standards: ISO 9001, ISO 19011, IATF 16949, and others
- Key requirements for an effective quality management system (QMS)
- Audit methodology: Plan, collect data, analyze, report, and follow-up
- Risk-based thinking in audits: Prioritizing high-risk areas for audits
- Auditing frameworks and models: Plan-Do-Check-Act (PDCA), Lean, Six Sigma, and more
- Case Study: Auditing a QMS for compliance with ISO 9001
Unit 3: Planning an Effective Quality Audit
- Defining audit objectives, scope, and criteria
- Selecting and training auditors for effective performance
- Planning the audit process: Pre-audit activities, scheduling, and resource allocation
- Developing an audit checklist and audit plan based on risk and priority
- Identifying key processes and stakeholders for the audit
- Communicating the audit process and managing expectations
- Case Study: Preparing for an external audit of a manufacturing organization
Unit 4: Conducting a Quality Audit
- Data collection techniques: Document reviews, interviews, observations, and sampling
- Auditing different types of processes: Operational, financial, technical, and management audits
- Interviewing and interacting with employees while maintaining objectivity
- Documenting audit findings and maintaining clear and accurate records
- Identifying non-conformities, weaknesses, and areas for improvement
- Handling resistance during audits and managing difficult situations
- Case Study: Conducting a quality audit in a service-oriented organization
Unit 5: Identifying Non-Conformities and Improvement Opportunities
- What constitutes a non-conformity: How to recognize and classify non-conformities
- Identifying areas of improvement: Waste, inefficiency, bottlenecks, and quality issues
- Using tools like Root Cause Analysis (RCA) to determine the root cause of non-conformities
- Establishing corrective and preventive actions (CAPA) based on audit findings
- Prioritizing non-conformities: Using severity and impact to determine action plans
- Reporting audit findings and making recommendations for continuous improvement
- Case Study: Identifying and addressing non-conformities in a product development process
Unit 6: Reporting and Documenting Audit Findings
- Structuring audit reports: Executive summary, findings, conclusions, and recommendations
- Communicating audit findings to different stakeholders (management, operations, compliance teams)
- Writing clear, actionable audit reports that facilitate decision-making
- Using visual aids: Graphs, charts, and dashboards to present data effectively
- Follow-up actions: Ensuring that audit recommendations are implemented and tracked
- Legal and compliance considerations in documenting audit results
- Case Study: Preparing a comprehensive audit report for senior management
Unit 7: Corrective and Preventive Actions (CAPA)
- Understanding CAPA and its role in improving quality management systems
- Developing corrective actions to address root causes of non-conformities
- Preventive actions: Identifying systemic issues and designing long-term solutions
- Documenting and tracking CAPA implementation to ensure effectiveness
- The CAPA process: Identifying, documenting, implementing, and verifying actions
- Using CAPA to promote a culture of continuous improvement across the organization
- Case Study: Implementing CAPA in response to a customer complaint audit
Unit 8: Auditing for Continuous Improvement
- Auditing as a tool for continuous improvement: How to drive organizational excellence
- Leveraging audits to assess the effectiveness of quality improvement initiatives
- Integrating quality audits with Lean, Six Sigma, and other process improvement methodologies
- Encouraging a culture of continuous improvement through regular audits
- Metrics and key performance indicators (KPIs) to measure the impact of audits on quality improvement
- Auditing as part of an overall quality strategy to achieve business goals
- Case Study: Auditing a continuous improvement program and measuring its success
Unit 9: Audit Follow-up and Ongoing Monitoring
- Importance of follow-up audits to ensure corrective actions have been implemented
- Ongoing monitoring and assessment of quality management systems
- Evaluating the effectiveness of quality improvements post-audit
- Strategies for sustaining improvements through periodic audits and reviews
- Managing audits in dynamic environments: Keeping pace with changes in technology, regulations, and business processes
- Case Study: Follow-up audits in a fast-changing industry such as tech or healthcare
Final Project and Action Plan:
- Participants will develop a quality audit plan for a specific process or department within their organization or a hypothetical case
- The project will involve creating an audit checklist, planning the audit process, conducting the audit, and reporting findings with recommendations for improvement
- Presentations of individual audit plans and findings, followed by group discussions and feedback
Final Assessment and Certification:
- Completion of the final project (audit plan and report)
- Active participation in case study discussions and exercises
- Certification awarded upon successful completion of the course and assessment
